The first recorded use of the word “Improvement” was in 1610. It comes from the Anglo-French word enprowment”, which meant “betterment” or “act of making better’’. According to the Oxford Dictionary, “Improvement” is defined as the act of becoming better than before or making something or somebody better than before. People do not like to keep doing the same things over and over; everyone wants to improve their life and their situation by continuously striving to become better. Without this it could be very difficult to even survive and live life to the fullest possible. The same principle applies to businesses. If they do not continuously improve, they risk becoming irrelevant pretty quickly. Through Continuous Improvement, a business can stay ahead of its competition and constantly improve its levels of excellence. Continuous Improvement is a never-ending effort to enhance all aspects of a business, leading to transformational results which helps a business stay ahead of the competition. It should be considered a strategic business approach as it aids in achieving the company’s strategic goals and moving it closer to its Vision.
Implementing a Continuous Improvement Strategy has great benefits:
- Delights Customers
- Improves Revenue
- Enhances Safety
- Enhances Product or Service Quality
- Reduces Defects, Wastes, and Costs
- Improves Delivery Performance
- Boosts Employee Morale by Increasing Engagement Levels and Collaboration
- Creates a Problem Solving/Learning Culture
- Enhances Brand Perception
History of Continuous Improvement:
Continuous Improvement has historical roots that can be traced back to various key milestones. In 1850, Eli Whitney introduced the concept of interchangeable parts. In 1900, Fredrik Taylor introduced Scientific Management, Time Study, and Work Standards. Frank Gilbreth contributed with Motion Study and Process Charts. Around the same time Lilian GIlbreth introduced Waste elimination and worker motivation methods.
Lean Manufacturing's History: The Origins of Lean
Lean Manufacturing’s history can be traced back to the production of the Ford Model T car in 1913 when Henry Ford relentlessly pursued waste elimination and improved flow through assembly lines which moved. This was integrated with human movement and parts supply. His efforts significantly improved productivity and time to assemble a car. Ford’s methods were replicated at GM around 1930. The Toyota Production System (TPS) was developed in the late 1940s, based on the concepts of Just In Time (JIT) and Jidoka (Intelligent Automation). These concepts trace their origin to observations by Sakichi Toyoda (the founder of the Toyota company). TPS has been built on the approach created by Sakichi Toyoda. Instrumental in this effort were the work of individuals like Sakichi Toyoda, Taichi Ohno, Kichiro Toyoda, and Shigeo Shingo. The term “Lean” was coined by James Womack in his 1991 book, “The Machine That Changed The World”.
The Origins of Six Sigma
Six Sigma has its origins dating back to 1809 when Carl Frederick Gauss introduced the concept of the Normal Curve. In the 1920s, Walter Shewhart introduced Statistical Process Control (SPC). Dr. W. Edwards Deming developed the Total Quality Management (TQM) methodology in the 1940s and 1950s. In the late 1970s, Matsushita (now Panasonic) took over Motorola’s TV sets unit and reduced defects dramatically, leading to Motorola’s serious commitment to quality. Dr. Mikel Harry and Bill Smith, often referred to as the father of Six Sigma, developed the Six Sigma Method in 1987 and applied it at Motorola.
Benefits of Implementing a Continuous Improvement Strategy
A Continuous Improvement strategy can be applied to any business or industry sector, as all businesses have processes. Continuous Improvement helps enhance these processes by eliminating non-value-added work, leading to the following benefits:
- Reduction in Lead Times: By improving the flow of products or services and reducing variation, lead times required to process customer orders are reduced, which benefits customers by reducing their need for excessive stock and working capital.
- Defect Reduction: It reduces the number of defects and the associated Cost of Poor Quality, enhancing brand image and increasing sales orders.
- Cost Reduction: Efforts to reduce waste and variation result in dramatic cost reductions and improved margins.
- Enhanced Employee Morale: Continuous Improvement empowers employees to simplify their work processes, solve problems, and work on initiatives that improve processes, which fosters a sense of value and leads to improved morale and reduced attrition levels.
- Identification of Voice of Customer (VOC): A clear understanding of VOC helps businesses deliver precisely what customers need, when they need it, with the right quality, and at the lowest delivered cost.
- Creation of an Open, Transparent Work Culture: Continuous Improvement encourages the daily surfacing and effective resolution of problems, creating a robust problem-solving culture.
Conclusion:
In conclusion, Continuous Improvement, when used as a business strategy, creates an environment where problems are solved in real time by addressing root causes. It helps identify weaknesses in business processes and human capital, employing appropriate methods for improvement. The benefits of Continuous Improvement are immense. At Peoplestrat, we have successfully transformed businesses by guiding them through holistic transformations. Contact us to learn more about Continuous Improvement and how you can embark on a Continuous Improvement journey.
About the Author
Deepak Bhaskar
CEO and Principal Consultant
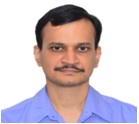
Deepak Bhaskar is the CEO and Principal Consultant of Peoplestrat, an International Management Consulting firm with over 100 years of combined experience in implementing Lean, Six Sigma and other Industry Wide Best Practices. Deepak has over 30 years of strong track record generating extraordinary performance in the Asia Pacific Region. He has managed Operations, Supply Chain, Lean Transformation and Centre of Excellence (CoE) with companies such as DuPont, Henkel, and 3M. He has extensive experience in Greenfield factory setup, factory consolidation, troubled plant turnarounds, and creating a sustainable culture of continuous improvement. Deepak has spent 9 years in Singapore managing the South East Asia region.